Blog post -
Aiming to Expand the Equipment Management Area that can be Handled by a Single Person - The Implementation and Benefits of IoT Tools
A comfortably air-conditioned environment and lighting that has been adjusted to the optimal brightness; high-rise buildings also reduce the stress of moving between floors via the use of high-speed elevators.
On the other hand, the building management staff must carry out the constant, demanding tasks of inspecting the equipment around the clock every day, recording the results on the inspection sheet, and using this information to compile reports.
In this article, we discuss how the promotion of DX in equipment management, including the introduction of IoT technologies, can help to reduce the burden on building management staff and solve these sorts of problems encountered in equipment management. We also spoke to Haga, who is in charge of equipment management at the Minato MIRAI Innovation Center, and Yamamoto, who is in charge of sales at the Tokyo branch office, about the energy savings that were achieved at the center.
Issues encountered in equipment management
--Please tell us about the issues that led you to attempt DX in equipment management, and any concerns you had regarding the introduction of IoT tools.
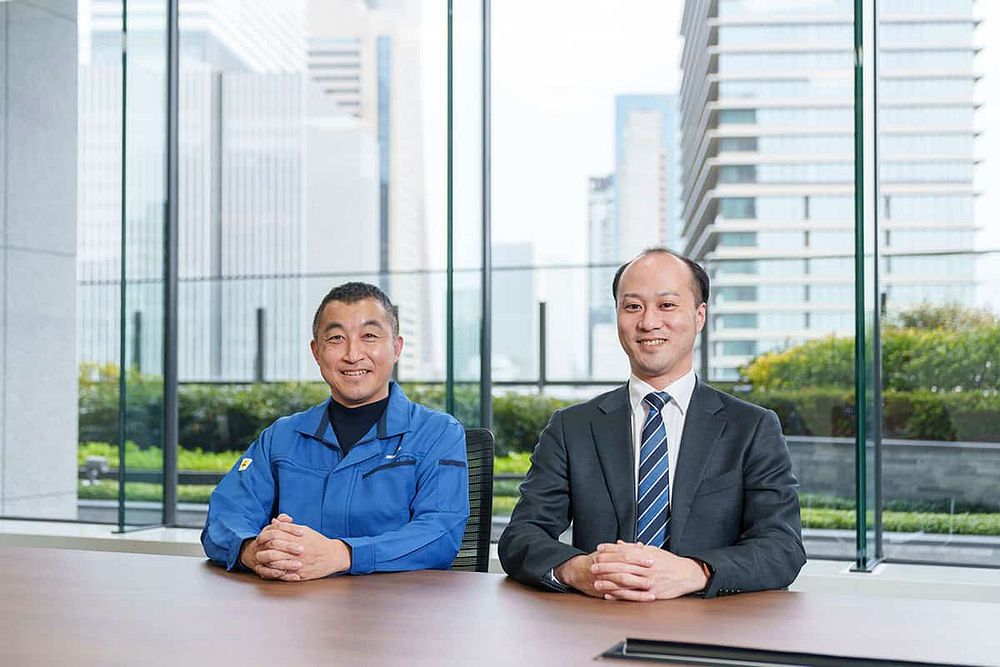
Labor shortages
Haga: In the equipment management sector, labor shortages are becoming chronic. Upon analyzing the working hours involved in maintenance work in equipment management, daily, monthly, and periodic inspections and dealing with problems and complaints accounted for 80% of the total work. In the case of daily inspections in particular, 87% of the time, people were required to go to the site, visually read the meters, and manually enter the meter readings. This burden was a problem that we could not ignore, especially as we had been facing a shortage of technicians for quite some time.
Issues regarding the introduction of sensors
Haga: When designing a building where it is not confirmed who the tenants will be, it is not clear at the design stage what kind of sensors and networks, etc., will be required for sensing. This only becomes known once the building is constructed and the tenants are decided. Installing sensors and networks in a completed building not only requires additional work, it is also expensive. Additional work also becomes essential if there are any sudden increases or changes to the desired sensing locations or data that you wish to capture.
Data utilization
Yamamoto: After installing sensors and connecting them to a network, the data collected must be analyzed and utilized in management. Data analysis is performed using analysis tools on a computer. However, there are many people in charge of building management who have never performed analysis, so it has become necessary to train and recruit people who are well-versed in the use of data.
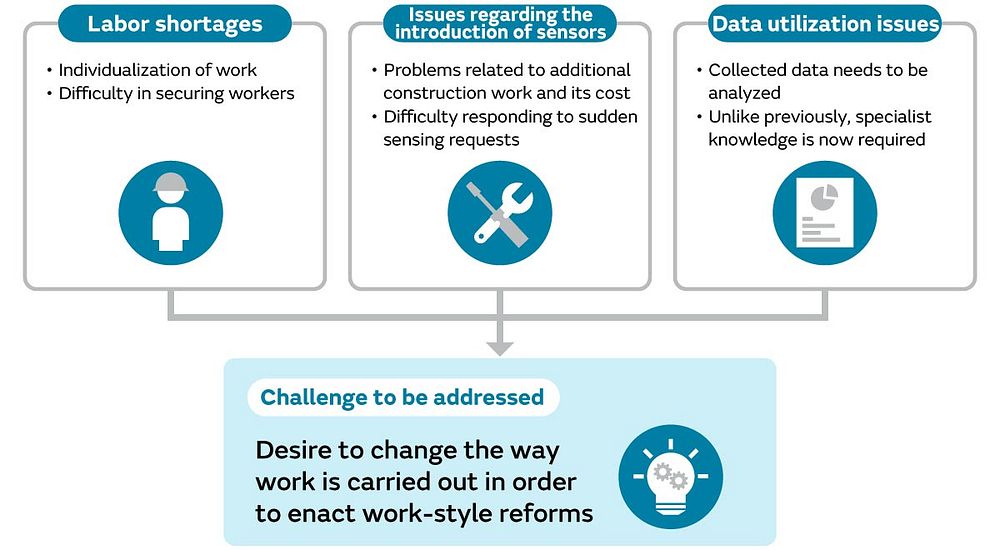
Benefits of DX in equipment management
--After overcoming various issues, you managed to achieve DX in equipment management. Can you tell us about the benefits you saw from DX?
Elimination of labor shortages and expansion of management area
Haga: Daily, monthly, and periodic inspections and dealing with problems and complaints account for 80% of our total work. Of this 80%, daily inspections make up 40% of the total. By introducing IoT tools, we were able to significantly reduce the time required for daily inspections, such as meter reading. Furthermore, as we were able to reduce the amount of time spent on daily inspections, that made it possible to expand the equipment management area that can be handled by a single person.
The benefits of introducing IoT tools
Yamamoto: In addition to installing control sensors in each of the different areas, we have also installed wireless sensors that measure the temperature and humidity. The sensor data is collected over a wireless network. In addition to obtaining the values from the sensors, we also take these values and visualize temperature discrepancies through heat maps to ensure the environmental conditions required by tenants. We have also introduced IoT tools on floors that require the same environment as in factories, such as electronic component research and development, allowing us to achieve the optimum environment for research and development. This helps to mitigate setbacks in research due to environmental deterioration, and therefore contributes to speedier development.
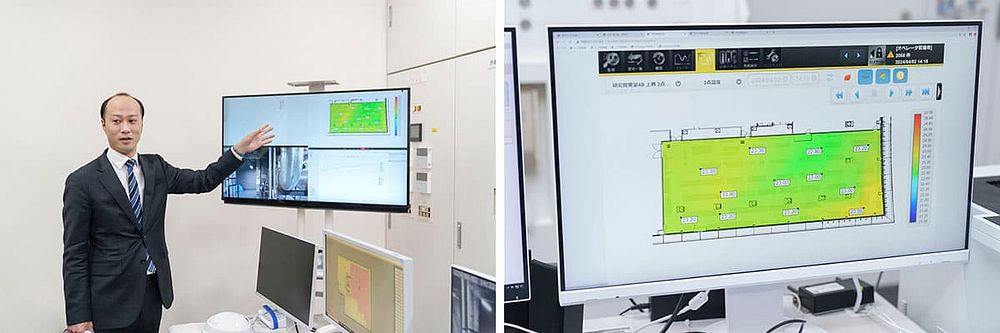
Disaster response
Haga: Murata's locations also suffered significant damage as a result of the 2011 Tohoku earthquake and tsunami. Taking what we learned from that experience, we have installed web cameras in various parts of the building and have adopted a system that can respond immediately to any emergency to ensure the safety of tenants. We also have a system in place that allows us to remotely stop and start equipment, which we can use in the event of a major disaster.
Responding to inquiries - troubleshooting
Haga: Even with sudden inquiries from tenants, such as malfunctioning air-conditioning or lighting, we aim to check the issue within 15 minutes, and deal with the problem within 30 minutes. As we believe that a speedy initial response is important, we set the alarm threshold values for the centrally monitored temperature and humidity, etc., to be stricter than the standard values, which allows us to address issues before users even make an inquiry or request a fix.
Issues related to promoting DX in equipment management
--DX for equipment management has many benefits, but there must also be various issues in attempting to implement it. What kind of issues did you encounter, and how did you resolve them?
Resistance to labor saving
Haga: I can't say that the possibility of labor saving was met with no opposition. However, the expansion of the management area that can be handled by a single person is a company-wide initiative and, for us, improving the efficiency of the ever-increasing inspection work was an urgent issue.
As I mentioned in my answer to a previous question, daily, monthly, and periodic inspections and dealing with problems and complaints account for 80% of our total work. Of this 80%, daily inspections make up 40% of the total. There was no objection to significantly reducing the time required for these daily inspections by introducing IoT tools.
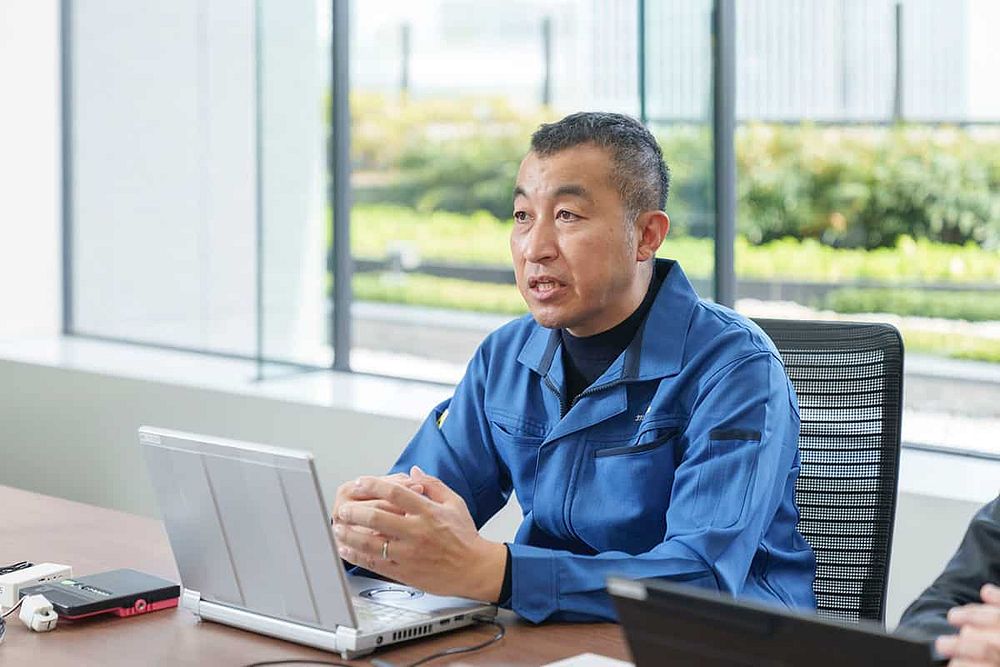
Additional construction work accompanying sensor installation
Yamamoto: Installing sensors, etc., in buildings that have already been constructed generally requires additional construction work, and the cost is not insignificant. However, using battery-powered wireless sensors and cameras that automatically read meters allowed us to minimize the additional work of adding power supplies and network cabling to the central monitoring equipment. Furthermore, the sensors are designed to be easily attached and detached, so we were able to select the best position for collecting data.
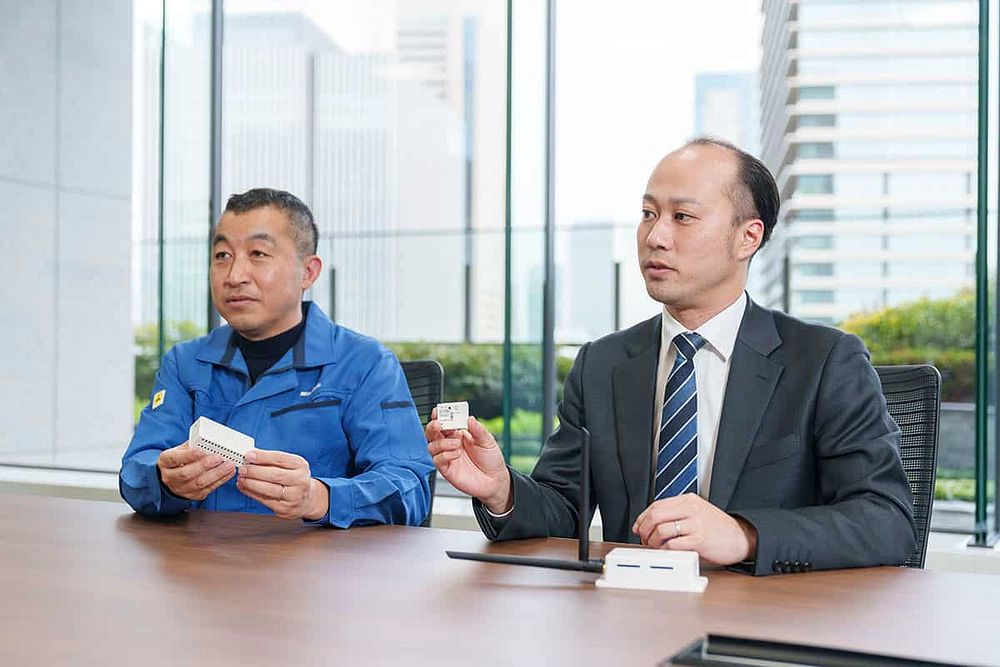
Utilization of collected data
Haga: There is no point in collecting data unless it is used for purposes such as optimizing energy consumption and predictive maintenance. However, in order to do that, knowledge of analyzing and interpreting data was required, which took time to learn. Therefore, we allocated the time the introduction of IoT tools saved on daily inspections and data entry to learning how to analyze and interpret data so that we could utilize it. Analyzing and interpreting data is a difficult area for staff who are used to more traditional means of equipment management. However, I think that being released from physically demanding and dangerous work is a major benefit.
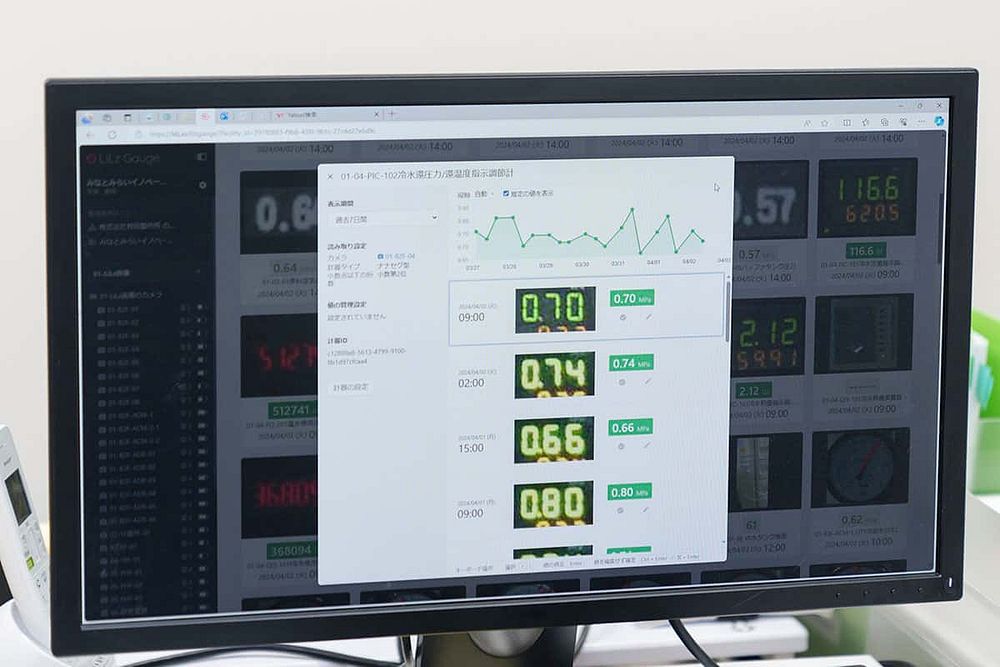
People-friendly equipment management
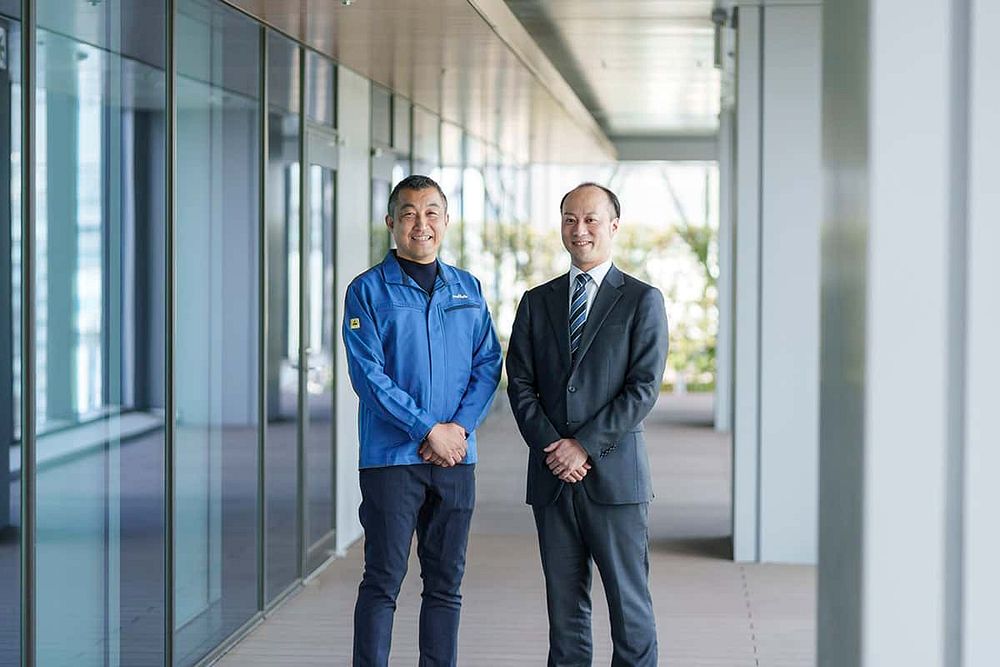
Haga: Our goal is to establish people-friendly equipment management. What we mean by "people-friendly" is work that is safe and secure. We want to eliminate the dangerous and demanding aspects of equipment management, shift to more sophisticated ways of working, such as analyzing and interpreting data, and eliminate occupational accidents. The aim is to then expand this endeavor to other locations.
Yamamoto: For example, we can use sensors to detect dangerous heating elements, use the heat map to identify points that need to be insulated, and apply thermal insulation to protect workers from the dangers presented by high temperatures.
Haga: In other words, people-friendly equipment management is an initiative that combines economic benefits, such as energy conservation and expanding the management area that can be handled by a single person, with efforts to protect workers from hazards, and increased motivation from engaging in more sophisticated work.