Pressmeddelande -
More power, new design: Schaeffler develops next-generation bipolar plates for fuel cell drives
- Fuel cell stacks with new metallic bipolar plates by Schaeffler exceed the power density of stacks made with previous-generation plates by about 20 percent.
- At a pilot plant in Herzogenaurach, Schaeffler is already making the plates for vehicle manufacturers to use in prototype and small-series production.
- Every aspect of the plate’s design has been engineered for maximum ease of transition to large-series production.
Arlandastad | August 22, 2023 | Schaeffler is demonstrating its development capabilities in the field of hydrogen-powered mobility with a new generation of metallic bipolar plates for PEM fuel cells. All fuel cell systems rely on bipolar plates. But the plates developed by Schaeffler feature a new design optimized for large-series production and leverage an innovative coating process for long fuel cell life. Moreover, stacks made using the new Schaeffler plates achieve a power density about 20 percent greater than that of stacks made using previous-generation plates. “When it comes to drive systems for commercial vehicles, Schaeffler is also investing in hydrogen, especially for long-haul applications. We are developing both individual components and complete subsystems for fuel cells and are gearing up for their full-scale industrialization,” said Matthias Zink, CEO Automotive Technologies at Schaeffler AG. At a purpose-built pilot production facility in Herzogenaurach, the company is now manufacturing the new plates in runs of up to several tens of thousands of units for use by international vehicle manufacturers in prototype and small-series production. The fully automated facility is part of Schaeffler’s center of excellence for hydrogen, a complex that also includes an extensive array of testing equipment. The facility has been designed so that it can also be used to manufacture large plates of the type used for electrolyzers. Schaeffler is thus ensuring both sustainable motion and the sustainable supply of green hydrogen. Thanks to its systems expertise, Schaeffler is also able to partner with customers to develop customized bipolar plates and components for fuel cell systems. Schaeffler is due to start production of bipolar plates under the name of Innoplate, a joint venture with Symbio, in Haguenau, France, at the start of 2024.
New plate design for increased power density
To the untrained eye, bipolar plates aren’t much to look at, being only about the size of a DIN A4 envelope and weighing just 60 grams. But they are core components of fuel cells, where they perform a number of vital functions, including providing channels both for the separation and distribution of the process gasses and coolant and for the removal of the water resulting from the chemical reaction. “Schaeffler has developed an innovative design that makes optimal use of the plate’s surface area,” explained Dr. Jochen Schröder, Schaeffler’s head of E-Mobility. “The finer and more precise the structures on the bipolar plate, the more efficient the plate is.” Schaeffler’s new plates enable a fuel cell stack power density of 4.6 kW per liter of fuel cell volume (including end plates and compression hardware).
For vehicle applications, several hundred of these plates are layered on top of one another, each separated by a membrane electrode assembly (MEA), to form a stack. The plates account for up to 80 percent of the stack’s weight, and up to 65 percent of its volume. Stacks comprising up to 400 of these cell units have a total power output of up to 140 kW – enough for light commercial vehicles. Heavy commercial vehicles up to 40 tons generally require two stacks.
Industrial-scale production
Schaeffler’s new generation of bipolar plates is also designed from the ground up for industrialization at large scale – an approach known as design for manufacturing (DFM). The aim is to achieve a level of cost-effectiveness and scalability of manufacturing sufficient for hydrogen-powered mobility to reach market breakthrough. In terms of production, the company is leveraging its many years of experience and expertise in metal stamping and forming, and has achieved the high level of precision needed to stamp the necessary ultrafine structures on the surface of the plates, which have a thickness of only 50 to 100 micrometers.
Another unique feature of the metallic bipolar plates made by Schaeffler is the coating system used. The purpose of coatings is to maintain a high level of electrical conductivity over the fuel cell’s entire service life. Schaeffler’s solution is “Enertect” – a family of high-performance coating systems developed specifically for bipolar plates. Depending on the customer’s requirements, the coatings can be engineered for maximum plate service life, minimum carbon footprint, or an optimized price-performance ratio. “Thanks to our capabilities in surface technology, we are able to offer each customer an application-specific coating solution. This means we can meet each customer’s requirements in terms of balancing cost, performance, and manufacturing-related CO2 emissions,” Jochen Schröder said. The coatings are applied using a specially adapted and fine-tuned version of the physical vapor deposition (PVD) process that Schaeffler has used successfully in the production of millions upon millions of highly stressed valvetrain components over the years. And finally, to make fuel cells gas- and watertight – vital from a quality and safety perspective – Schaeffler uses either injection-molded or silk screen gaskets, or, depending on requirements, a special laser welding process developed in-house.
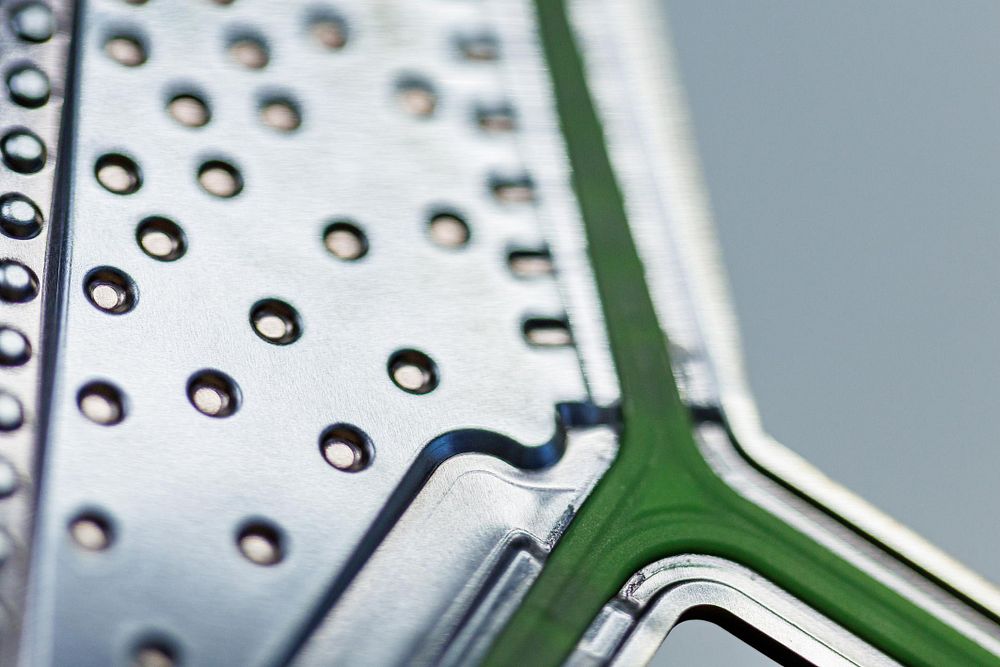
Visit Schaeffler at the 2023 IAA Mobility show in Munich: At this year’s IAA Mobility show at the Munich Exhibition Center, Schaeffler is exhibiting a whole range of new technologies for sustainable, efficient and comfortable mobility. These include solutions for inner-city goods delivery using e-cargo bikes, a new type of steering system, high-efficiency electric and hydrogen drives, new mobility concepts, and more.
Schaeffler press conference: Monday, September 4, 2023, 11:00 a.m. to 11:20 a.m. (CEST): Klaus Rosenfeld, CEO of Schaeffler AG, and Matthias Zink, CEO Automotive Technologies at Schaeffler AG, will address the media at the Schaeffler showcase at Booth B40 in Hall B3 and online via live stream.
Schaeffler at the IAA Conference:
- Wednesday, September 6, 2023, from 4:00 p.m. to 4:45 p.m., Main Stage, Hall A1. Session: “Towards a Sustainable Automotive Value Chain – Ambitions, Challenges & Collaboration.” Speakers include Matthias Zink, CEO Automotive Technologies, Schaeffler AG.
- Thursday, September 7, 2023, from 3:00 p.m. to 3:45 p.m., Visionary Clubhouse, Hall A2. Session: “Here to innovate: revolution needs cooperation! Disruptive thinking, new technologies, new vehicle concepts – partnerships as enablers for innovation and change”. Speakers include Ralf Busse, mocci | CIP MOBILITY GmbH; Kersten Heineke, McKinsey Center for Future Mobility; Dennis Müller, Enchilada Franchise AG; and Claus-Dieter Schilling, Schaeffler.
Schaeffler and mocci are also teaming up for the IAA Experience at the IAA Summit in Hall A3. There, on the Cycling & Micromobility Course, visitors will be able to test-ride mocci e-cargo bikes featuring drive technology by Schaeffler. The IAA Experience is open from 9:00 a.m. to 6:00 p.m. daily from September 4 to August 8.
Ämnen
Kategorier
Schaeffler Group – We pioneer motion
Schaeffler Group har drivit fram banbrytande uppfinningar och utvecklingar inom området rörelseteknologi i över 75 år. Med innovativa teknologier, produkter och tjänster inom elektrisk mobilitet, CO₂-effektiv drivning, chassilösningar, Industri 4.0, digitalisering och förnybar energi är företaget en pålitlig partner för att göra rörelse mer effektiv, intelligent och hållbar – under hela livscykeln. Rörelseteknikföretaget tillverkar högprecisionskomponenter och system för drivlinor och chassiapplikationer samt rullnings- och glidlagerlösningar till ett stort antal industriella applikationer. Schaeffler-gruppen omsatte 15,8 miljarder EUR 2022. Med cirka 84 000 anställda är Schaeffler-gruppen ett av världens största familjeägda företag. Med mer än 1 250 patentansökningar 2022 är Schaeffler Tysklands fjärde mest innovativa företag enligt DPMA (tyska patent- och varumärkesmyndigheten).