Press release -
Heavy Trench Covers Are History
Once in a while, a product will come along whose performance will drive a change in standards across entire industries. Like stainless steel. Or concrete. Or a trench cover which is (typically) 65% lighter than the cast iron traditionally used, eliminating the need for costly specialised lifting equipment and the accompanying health and safety hazards. And, unlike metal and concrete infill covers, it’s engineered from a GRP composite material which is inert and impervious to corrosion from water and salt, as well as many other corrosive constituents.
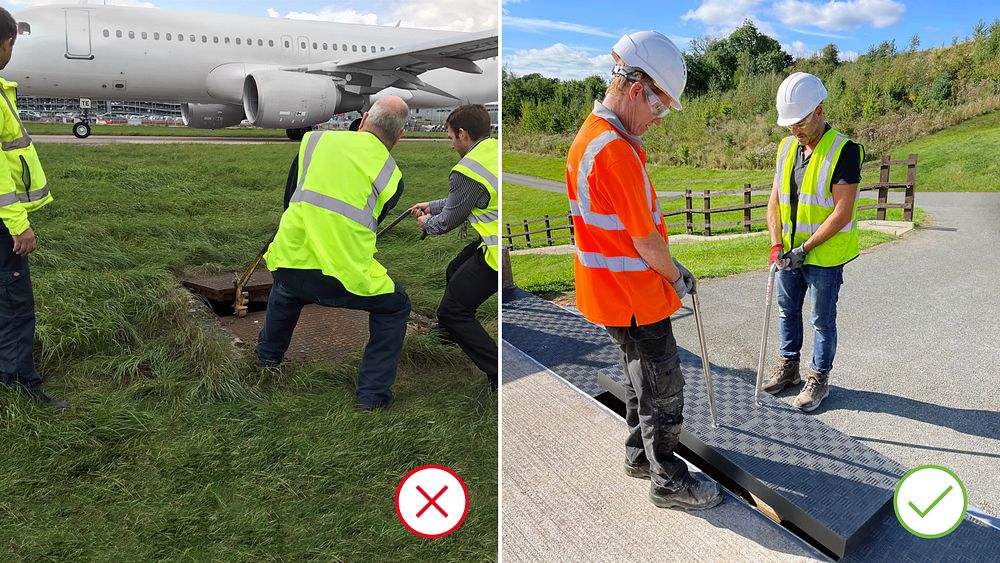
(Left) heavy metal trench covers come with inherent H&S hazards & often require specialised lifting equipment
(Right) lightweight Fibrelite GRP trench covers eliminate manual handling risks
Changing The Standard For Health & Safety
Fibrelite’s GRP composite trench and manhole covers are fast usurping metal and concrete covers to become the standard for high-performance industries like airports, commercial ports, leisure cruise terminals, military and defence, power generation (both traditional and renewables), and data centres, with companies like Magnox, The National Grid, all branches of the UK armed forces, and the world’s largest technology brands specifying Fibrelite covers for new build and retrofit projects.
Recent Installation: Port Cruise Terminal Upgrade, UK
As part of this Southern English Port’s cruise terminal upgrade project, Fibrelite was approached by the end-user, who was providing the Onshore Power Supply (OPS) systems. The port had previously considered installing cast iron trench covers to cover the 500 metres of trench housing the high-voltage power cables, but due to their weight (approximately 350 kg) and the additional associated overheads, they approached Fibrelite for a lighter alternative.
Fibrelite developed a bespoke covering solution made up of dozens of custom-sized F900 (90-tonne) load-rated GRP composite trench covers in varying dimensions to suit the specified trench rebate dimensions. The Fibrelite covers are light enough for safe removal with the site dolly, complying with the load rating requirement of the site. Fibrelite’s GRP composite covers are typically 65% lighter than traditional cast iron and reinforced concrete covers.
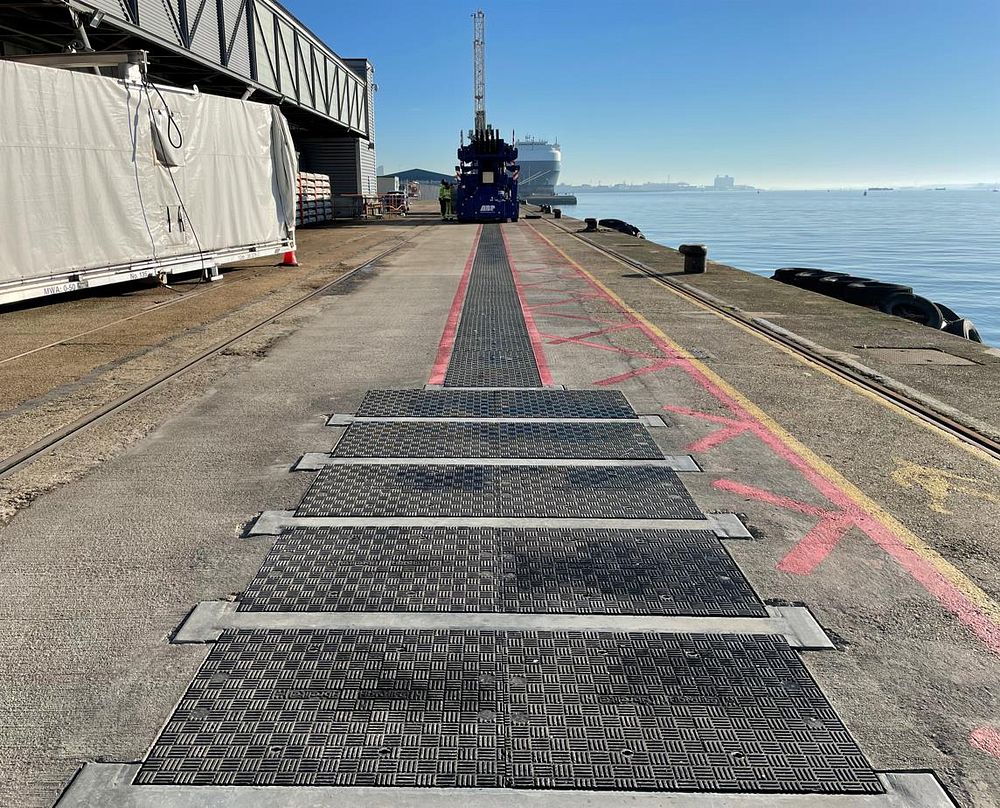
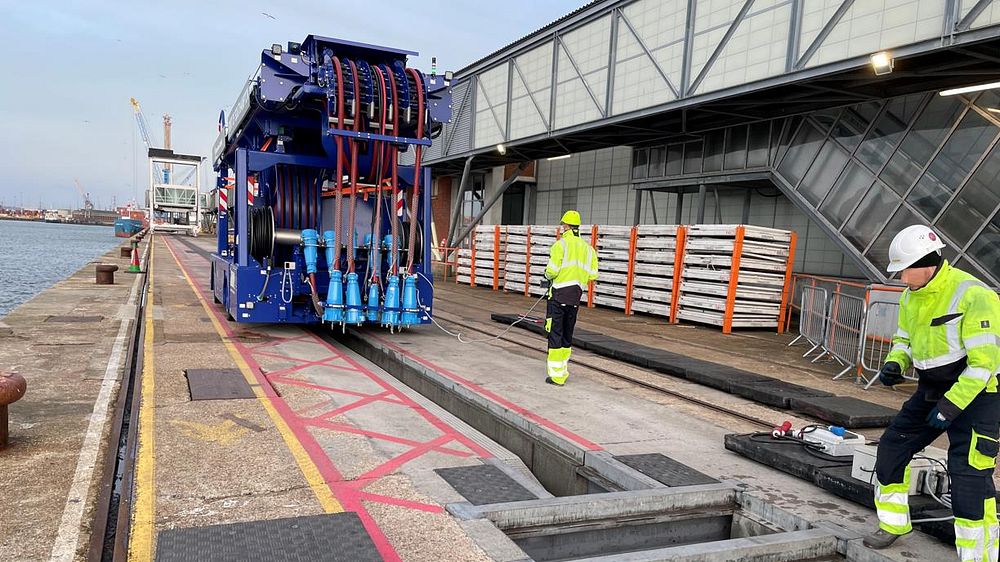
Fibrelite covers are typically 65% lighter than traditional cast iron and reinforced concrete
Recent Installation: Major Southern UK Airport Off-Apron Lighting Pit Upgrade
At one of the UK’s busiest airports, Fibrelite designed and manufactured a retrofit replacement for manhole covers over off-apron runway lighting pits where onsite staff have a window of approximately two minutes to effect maintenance and/or repair works between take-offs and landings, including removing and replacing the F900 load rated access cover. The new lightweight GRP composite Fibrelite covers now allow safe, fast access to the lighting pits, maximising time for maintenance and minimising the risk of injury.
A Bright Future For Fibrelite
I’ve been a part of the Fibrelite journey since 2016, and it’s been exciting to play a part in driving the upgrade from traditional concrete and metal trench and manhole covers to GRP composites in myriad industries, especially those where manual handling is critical, and seeing how we’ve helped increase health and safety and performance in those industries. We expect to see more and more industries make the upgrade to Fibrelite composite covers, especially in mission-critical areas.
Aaron McConkey, Marketing Manager, Fibrelite
Explore Fibrelite’s technical case study library here: https://fibrelite.com/all-case-studies/
Related links
Topics
- Architecture
Categories
- composite
- fibrelite
- grp
- frp
- access
- manual handling
- health & safety
- trench covers
- commercial ports
- airports
Fibrelite is a global manufacturer of highly engineered Glass Reinforced Plastic (GRP) composite manhole and trench access covers capable of taking up to 90-tonne loads while still light enough to be removed manually by one or two people using Fibrelite’s ergonomically designed lifting handles. In 1980, Fibrelite designed the world’s first composite manhole cover, eliminating manual handling and other health and safety issues associated with traditional metal covers. Today, Fibrelite continues pioneering composite technology, continually innovating to solve customers’ challenges across the globe.
Initially developed over 40 years ago, Fibrelite remains the composite access cover of choice for projects worldwide, from data centres and high-tech manufacturing facilities to infrastructure, transport and stadia. Fibrelite covers are increasingly specified for both new build and retrofit projects across a variety of industries in more than 80 countries.
Since 2013, Fibrelite has been a part of OPW (a Dover company) allowing them to offer an unprecedented portfolio of complementary best-in-class products.
For more information, visit the Fibrelite website at www.fibrelite.com